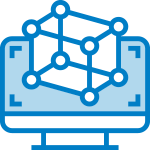
INGENIERÍA
Nos avalan 15 años de experiencia en el diseño e industrialización de productos electrónicos en diferentes sectores, para todo tipo de clientes. Desde dispositivos electrónicos o wearables para uso cotidiano hasta grandes proyectos a gran escala para la optimización de procesos industriales, somos una ingeniería abierta a cualquier proyecto.
IoT, Big data, realidad virtual, sistemas inteligentes, aplicaciones industriales a gran escala, comunicación inalámbrica… Gracias a nuestras propias líneas de producción y coating, y a un extenso dominio del ecosistema tecnológico actual y de las herramientas para la industria 4.0, nuestra ingeniería actúa como un auténtico booster para colaboradores y otras empresas de su entorno.
A través de la ingeniería multinivel, para un mismo proyecto son muchos los actores que pueden verse beneficiados a lo largo de su desarrollo, tanto vertical como horizontalmente. Descubre por qué Bizintek lo hace posible.
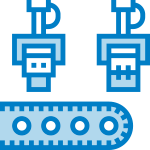
SOPORTE EN LA FABRICACIÓN DE PRODUCTOS
Mientras otras ingenierías se centran en desarrollar un concepto más “rígido” del producto, nuestra dinámica de trabajo se despliega en todos los niveles, y actúa como fuente de optimización en diferentes etapas de la industrialización de un dispositivo o del desarrollo de un proyecto.
¿Cómo lo hacemos? Si un proyecto requiere de un servicio tecnológico específico o de un análisis técnico para salir adelante, la ingeniería multinivel que es nuestra especialidad.
Nuestros equipos de trabajo realizan un estudio detallado que permite involucrar distintas fases del proceso industrial en el desarrollo de un proyecto, con el fin de mejorar todas las características posibles.
- Análisis de BOM: obsoletos – alternativas – plazos – costes.
- Informe de fabricabilidad: Mejoras de diseño – Reducción de errores – Mejora de costes – Fiabilidad.
Prácticamente ninguna empresa del sector ofrece este nivel de precisión en sus investigaciones previas a la industrialización de un dispositivo.
¿CÓMO TRABAJAMOS?
Con nuestra experiencia somos capaces de realizar los análisis necesarios y demostrar la importancia del control de cada parte del proceso.
Analizamos los diseños y realizamos propuestas de mejoras aportando soluciones para ofrecer los mejores resultados.
Desarrollamos los proyectos junto al cliente.
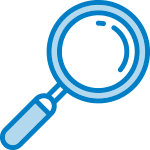
Paso 1: BOM y valoración de alternativas
Aplicamos nuestra experiencia como diseñadores de productos electrónicos para ofrecer a nuestros clientes de producción los mejores resultados. Antes de industrializar realizamos un estudio del BOM para analizar posibles mejoras, alternativas y reducciones de precios sobre los componentes, así como un detallado estudio del ciclo de vida del BOM (componentes obsoletos o no recomendados para nuevos diseños).
Por otro lado, los plazos de componentes electrónicos están creciendo continuamente. Por eso es cada vez más importante contar con alternativas validadas. En este aspecto, también ayudamos a nuestros clientes en la búsqueda de referencias cruzadas de sus componentes desde un principio o bien en caso de roturas de stock
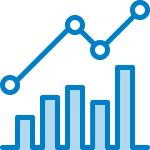
Paso 2: Revisión y propuestas de optimización
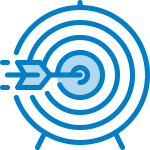
Paso 3: Puesta en marcha
En este punto todo nuestro equipo tiene un objetivo claro, tenemos una meta que cumplir y unas pautas que seguir para alcanzarla con éxito. Para ello debemos ser extremadamente eficientes porque la eficiencia es la base de la calidad y la reducción de costes.
La documentación final es introducida en nuestro ERP cruzando las referencias necesarias con los empaquetados o acabados más óptimos para cada ocasión, los listados de materiales y sus especificaciones pasa por nuestros controles y son inmediatamente direccionados a los proveedores. Proveedores homologados previamente en los que depositamos nuestra confianza y a los que les hacemos un seguimiento constante.
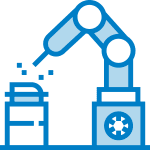
Paso 4: Producción
Para cada producto definimos los procesos técnicos más adecuados. Confiamos en los procesos automatizados y controlados por la experiencia y el know-how de nuestro equipo que constantemente supervisa los procesos del equipo auditando cada paso.
El proceso comienza en la dosificación de pasta donde están detectados aproximadamente el 70% de los defectivos de producción. Cada producto requiere una programación de impresión diferente, en cada una de ellas, nuestros técnicos valoran el tipo de pasta de estaño y las herramientas a utilizar variando el flujo, las presiones y las alturas en función del resultado deseado.
Los utillajes para la dosificación del estaño son parte de nuestro análisis previo ya que las aperturas son críticas en esta parte del proceso y nos ayudamos de nuestros avanzados conocimientos en los distintos tipos de acabados con electropulido, multilevel…
Tras el montaje en nuestras pick&place de última generación, no podemos olvidar de la importancia de un buen perfil de soldadura porque el proceso requiere un control muy exhaustivo para evitar los choques térmicos y alcanzar un buen mojado respetando las curvas de cada componente, llegando a un compromiso entre todos ellos.
El 100% de la producción es por otro lado analizado por nuestro equipos de inspección 3D.

Paso 5: Test y ensamblado
En el terreno de ensamblado mecánico contamos con las herramientas necesarias entre las que destaca la tecnología de fabricación aditiva para utillajes de proceso facilitando su montaje y reduciendo una vez más los costes implicados y acelerando el time to market.

¿Quieres optimizar tu diseño?
Podemos ofrecerte un análisis detallado de tu producto y ofrecerte alternativas para mejorar la fabricación y reducir los costes de producción